Lightweighting is one of the biggest challenges facing automotive manufacturers.
Multi-material vehicles that incorporate lighter materials such as aluminum, carbon-fiber composites, high-strength steel, magnesium, titanium, and various types of foam, plastic and rubber are no rarity anymore.
They become increasingly important in order to for instance offset heavy batteries in electric cars. SaarGummi’s assembly process such as modular sealing systems and partial and full TPE applications might become even more relevant. The following examples shall inspire to further rethink conventional processes, materials and products.
Material Joining with TSS Technology
The power train still remains a focus area for vehicle lightweighting efforts, with the chassis running a distant second, but interiors are growing as a lightweighting target. Many assembly equipment vendors have recently unveiled products that address some of those lightweight material joining challenges. For instance, engineers at Weber Screwdriving Systems Inc. developed TSS technology.
Designed for plastic and composite material joining, TSS can be used on similar or dissimilar materials. During the TSS joining process, plastic components are melted, creating a thermal adhesive bond. It allows engineers to place plastic bosses in sandwich structures, which consist of a honeycomb or foam core with outer layers of fiber-reinforced plastics. “The technology essentially controls the fastening parameters through rotational speed, Z-axis speed, and what’s known as torque and depth gradient,” explains Tom Rougeux, regional sales director at Weber Screwdriving Systems.
Photo source: BMW Press
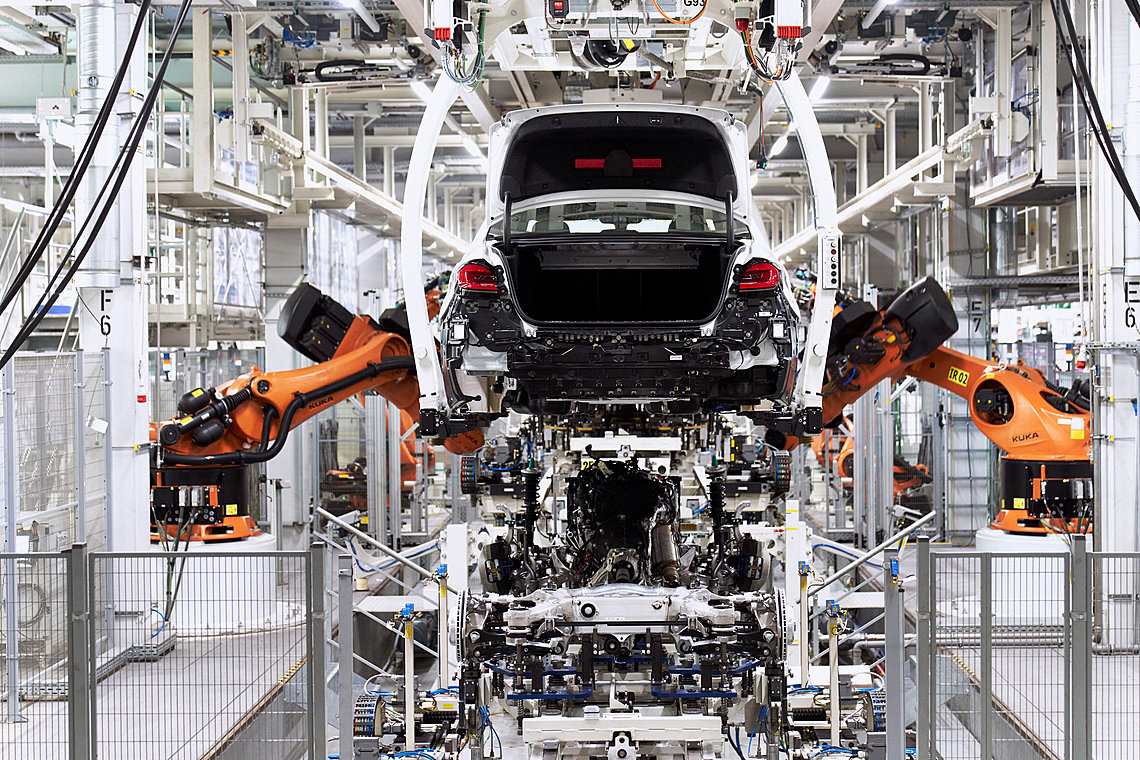
Reversive Bonding Process
Another innovative assembly process is developed at the American Chemistry Council and Michigan State University. Engineers created a “reversible” bonding process. “Ferromagnetic nanoparticulate electromagnetic glue involves nanosized spheres of iron inside a polymer,” says Mahmoodul Haq, engineering professor at Michigan State University. “When alternating electric current changes the magnetic field rapidly, the nanoparticle balls vibrate. Vibration causes friction, causing the polymer temperature to rise 400 to 800 F within seconds.” Mike Day, a technical consultant at the American Chemistry Council says,“The bonding agent has been shown to work when joining dissimilar materials, such as aluminum to steel and steel to composite.” He claims, that “This bonding technology could revolutionize the auto industry by giving us the ability to bond, unbond and strengthen structural parts in a way that helps keep weight down and changes the way we think about joint fatigue altogether.”Plastics
3-D Printed Cars
distributed, smaller manufacturing facilities, using far fewer parts due to a prognostic future of rapid customization and personalization of cars: going from unique design, computer modeling, to building (printing) in days, not years. This new manufacturing model may also lead to further improvements in sustainability.
Photo source: BMW Press
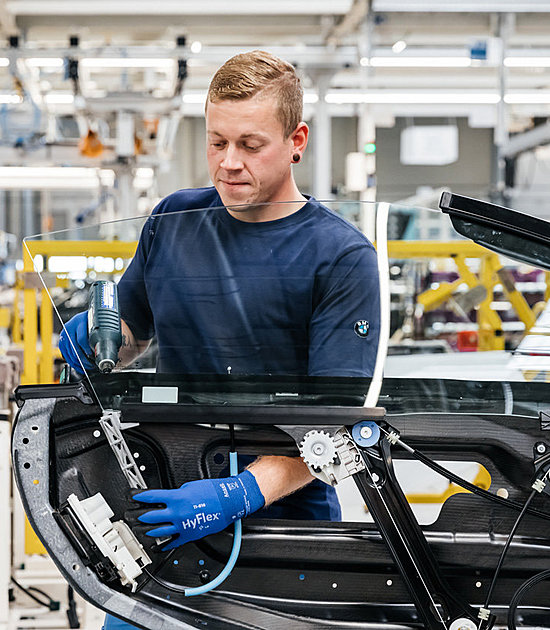
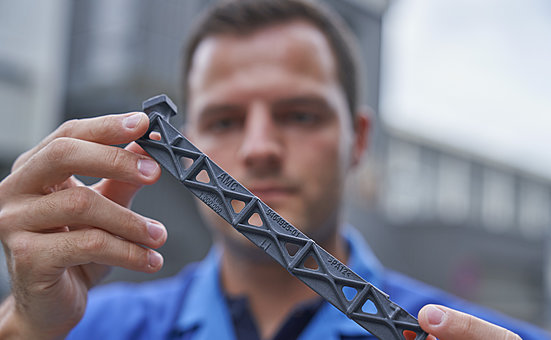
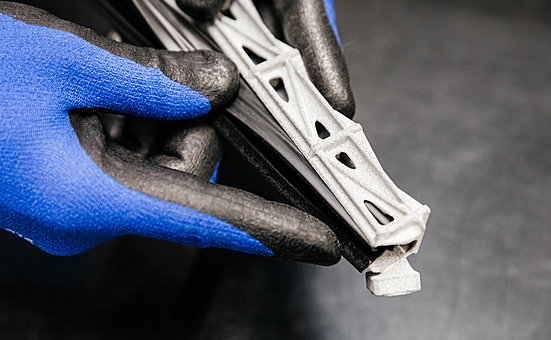
Example “Olli”
OLLI is a self-driving electric vehicle built with 3-D printing technology used on public roads in the Washington, DC, area. The composite material used for the vehicle is 80 percent acrylonitrile butadiene styrene (ABS) plastic and 20 percent carbon fiber.
OLLI seats multiple people for a ride sharing experience that integrates the advanced cognitive computing capabilities of IBM Watson. Riders hop in and ask for recommendations for dinner or a sightseeing spot and then sit back and relax as OLLI takes them there. In addition to being lightweight and efficiently powered, many parts can be recycled at the end of OLLI’s lifespan—which means OLLI could represent the future of eco-friendly public transit.
Example “Ford”: Car Parts Made Out of Thin Air
Ford has announced plans to make auto parts using plastics made in part from captured carbon dioxide waste streams. Ford says the CO2 will be used as a feedstock to make foam plastics for use in seat cushions, seat backs, floor mats, and other components such as side paneling and consoles. Ford researchers say they were inspired by plants that take in carbon dioxide and create complex sugars. In a similar vein, Ford is taking excess carbon dioxide and making durable plastics to use in vehicles. Even though it’s not sugar, the researchers said: “We think it’s pretty sweet.”
Flax seed fibers and PLA
The Lina electric car built by TU/Ecomotive, a student team from the Eindhoven University of Technology in the Netherlands, is a great example of the next generation of material innovations. The car’s body is manufactured from a bio-based composite resin made from flax seed fibers and polylactic acid (PLA).
Another downside of this technology is the physical property of the resin, which tends to break despite having a high strength-to-weight ratio.
Future?
Aluminium and carbon fibers, currently the two major lightweighting agents, are expensive to work with and further increase future auto repair costs. Flax fibers, plastics, 3D printed materials all still somewhat under scrutiny due to their structural challenges. But despite this criticism, there are some recent successful productions and launches of lightweight cars on the market. The latest two examples are the 2020 BMW M2 CS and Riversimple’s Rasa, which are expected to hit large-scale production and commercial launch in 2020.